Die cut mylar bags have become increasingly popular in various industries, from food and beverage to cosmetics and electronics. Their ability to be customized into unique shapes and sizes, combined with mylar's excellent properties such as moisture resistance, oxygen barrier, and durability, makes them a top choice for product packaging. This article will walk you through the entire process of making die cut mylar bags, from initial planning to the final product.
Understanding Mylar Bags
Mylar is a brand name for a type of biaxially oriented polyester (BOPET) film. When used to make bags, it offers several advantages. Mylar is highly resistant to moisture, which helps keep products dry and free from mold and mildew growth. It also provides a strong barrier against oxygen, preventing oxidation that can spoil food, degrade the quality of cosmetics, or damage sensitive electronics. Additionally, mylar has good tensile strength, meaning it can withstand handling and transportation without tearing easily.
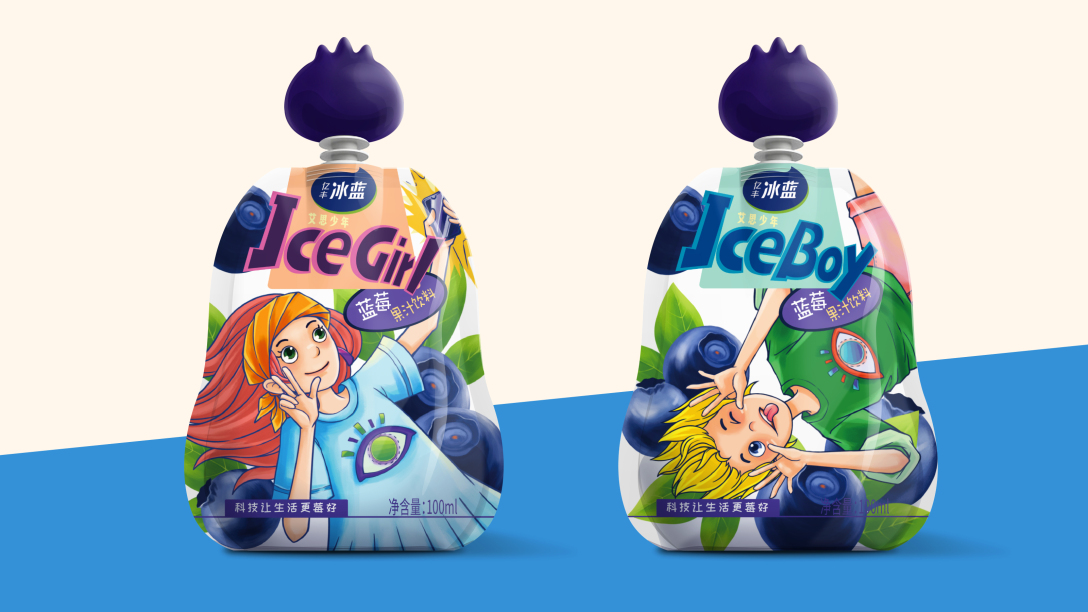
Step - by - Step Process of Making Die Cut Mylar Bags
1. Determine the Bag Dimensions
The first step in creating die cut mylar bags is to accurately determine the dimensions. Measure the product that will be packaged. Consider not only the length, width, and height but also any irregular shapes or bulges. For example, if you're packaging a uniquely shaped snack, make sure the bag has enough room to accommodate it without being too large, as excess space can lead to product movement and potential damage. Also, factor in any additional space needed for things like resealable zippers or hang holes if those features are part of your design.
2. Select the Appropriate Mylar Film
Choose the right thickness of the mylar film based on your product requirements. Thicker mylar films, such as 7 - 10 mil, offer greater durability and puncture resistance. This is ideal for products that may be handled roughly during transportation or storage, like heavy hardware items or products with sharp edges. Thinner films, around 3 - 5 mil, are more cost - effective and provide flexibility. They are suitable for lightweight products such as dried herbs, spices, or small electronic components. You should also consider the finish of the mylar film. Matte finishes can give a more elegant, sophisticated look, while glossy finishes make colors appear more vibrant and can attract attention on store shelves.
3. Design the Artwork
Use graphic design software like Adobe Illustrator or CorelDRAW to create the artwork for your die cut mylar bags. Incorporate your brand logo, product information, and any eye - catching graphics or patterns. When designing, keep in mind the die lines, which are the lines that indicate where the mylar will be cut. These lines should be clearly marked in a separate layer in your design file. Ensure that all text and important graphics are within the safe zone, away from the die lines, to avoid being cut off during the manufacturing process. Also, consider the printing method you'll be using. If it's digital printing, your design can have high - resolution, full - color images. For flexography, which is more common for large - scale production, simpler designs with fewer colors may be more cost - effective.
4. Prepare the Die Cutting Tools
A custom cutting die is essential for creating the precise shapes of your die cut mylar bags. Work with a reputable die - making company to design and manufacture a die that matches your desired shape. The die is typically made of sharp steel and is designed to cut through the mylar film cleanly. When choosing a die - maker, look at their portfolio of previous work, customer reviews, and their ability to meet your specific requirements in terms of shape complexity and accuracy. Some die - making companies also offer 3D modeling services, allowing you to visualize the die and the resulting bag shape before production.
5. Source the Mylar Film
Once you've finalized your design and die, it's time to source the mylar film. You can purchase mylar film in rolls from various packaging material suppliers. Ensure that the supplier provides high - quality film that meets your specifications in terms of thickness, finish, and any additional properties you may need, such as anti - static or UV - resistant features. Request samples from potential suppliers to test the film's quality and compatibility with your printing and die - cutting processes.
6. Printing (Optional but Recommended)
If you want to add printed graphics to your
die cut mylar bags, this step comes next. There are several printing methods available for mylar film. Digital printing is great for short - run production and allows for high - quality, full - color prints with detailed images. Flexography is more suitable for large - scale production and offers good color consistency. Gravure printing can also be used for high - volume orders and provides excellent print quality, especially for smooth gradients and fine details. Before starting the printing process, make sure the mylar film is properly pre - treated. Some films may need to be surface - treated to improve ink adhesion. The printing process should be carefully monitored to ensure accurate color reproduction, sharp images, and consistent print quality across all bags.
7. Die Cutting
After printing (if applicable), the mylar film is ready for die cutting. Place the mylar film on the die - cutting machine, aligning it precisely with the cutting die. The die - cutting machine applies pressure to the die, cutting the mylar film into the desired shape. The machine can be adjusted for different levels of pressure depending on the thickness of the mylar film. During the die - cutting process, it's important to check for any mis - cuts, jagged edges, or other defects. If there are issues, the machine settings may need to be adjusted, or the die may need to be repaired or replaced.
8. Bag Assembly
Once the individual die - cut pieces are created, they need to be assembled into bags. This usually involves heat - sealing the sides and bottom of the bags. A heat sealer is used to apply heat and pressure to the edges of the mylar, melting the plastic and creating a strong, airtight seal. The temperature and pressure settings on the heat sealer should be adjusted according to the thickness of the mylar film. For bags with additional features like resealable zippers or spouts, these components are attached at this stage. Make sure that all seals are properly formed and that the zippers or spouts are functional.
9. Quality Control
Perform a thorough quality control check on the finished die cut mylar bags. Inspect each bag for any visual defects such as cuts in the wrong place, uneven seals, or smudged printing. Check the functionality of any additional features, like the ease of opening and closing a resealable zipper. For bags intended for food packaging, ensure that they meet all relevant food - safety regulations. Randomly select a sample of bags and test their strength by gently pulling on the seams to make sure they can withstand normal handling.
10. Packaging and Storage
After passing the quality control check, the die cut mylar bags are ready to be packaged. They can be packaged in bulk, usually in large boxes, or individually wrapped depending on your requirements. Store the bags in a cool, dry place away from direct sunlight and heat sources. This helps maintain the integrity of the mylar film and ensures that the bags are in good condition when they are needed for product packaging.
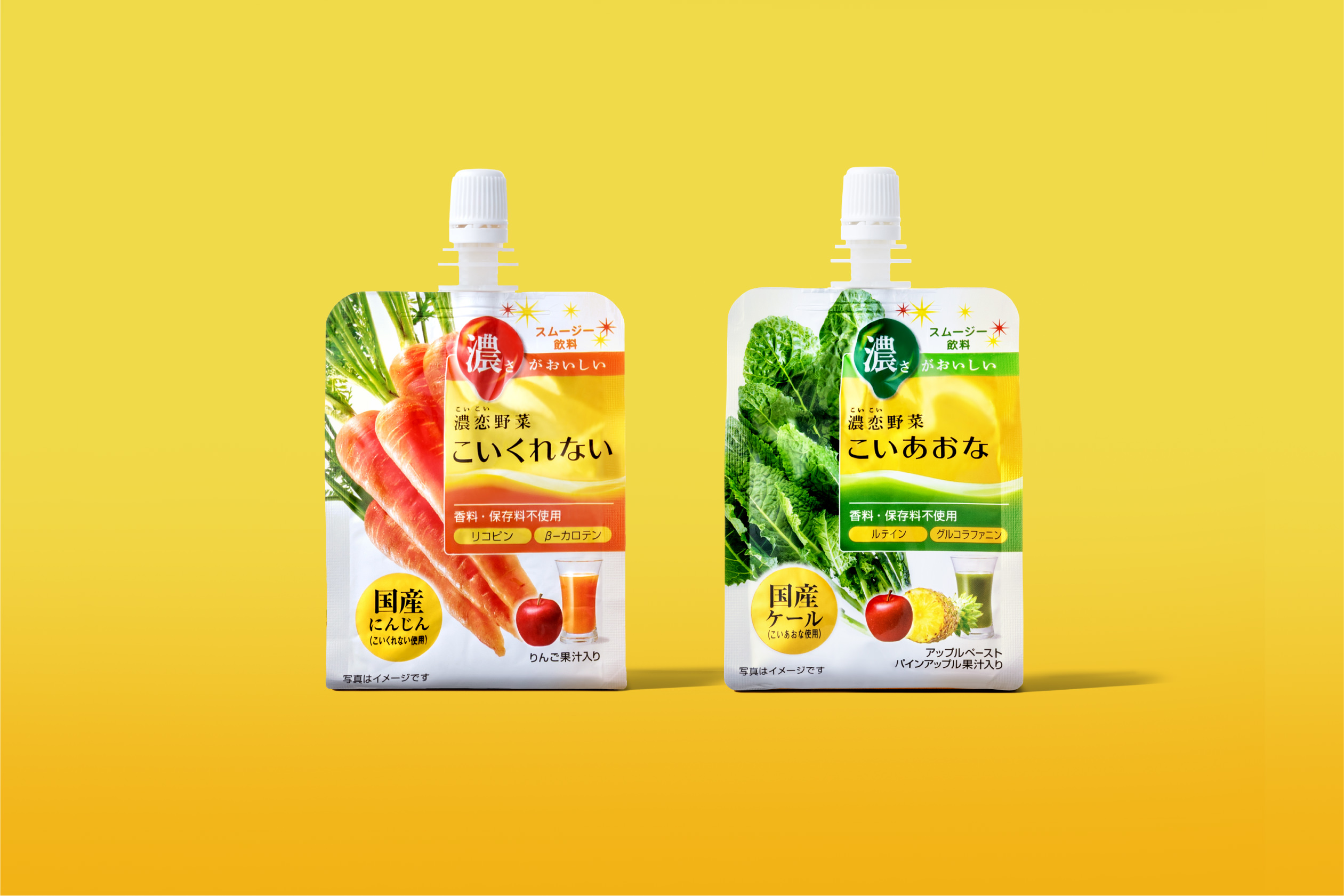
Conclusion
Making
die cut mylar bags requires careful planning, the right choice of materials and tools, and attention to detail at every step of the process. By following these steps, you can create high - quality, customized die cut mylar bags that not only protect your products but also enhance your brand image and stand out in the marketplace. Whether you're a small - scale entrepreneur or a large - scale manufacturer, understanding this process can help you make informed decisions and produce packaging that meets your specific needs.
die cut bags with logo
die cut bags with your logo
are mylar bags smell proof